Ceramics thermal energy storage
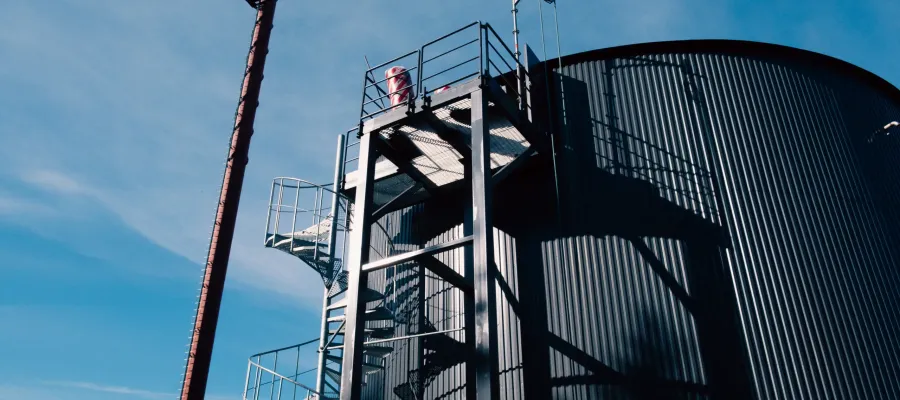
Wouldn’t it be amazing to live in a more just and equal society where extreme poverty and hunger are a thing of the past? A future in which our species is not exploiting its environment to the point of tipping the whole planet off balance? The energy transition should be and could be a step in that direction and renewables are a big part of this transition.
TES systems basics
An issue solar technologies face is the intermittency of the sun’s shining, which makes them produce energy discontinuously. The solution best suited to deal with this intermittency in the case of concentrated solar collectors is called thermal energy storage (TES), and we discussed it in depth in our previous publications (one and two).
Figure 1: Schematic of a molten salt storage system with two tanks. Source.
The spark notes on sensible heat storage, the type of TES we’ll focus on the most in this article, are that we heat up a material that can absorb a lot of heat without changing its phase and keep it in a well-insulated vessel. The most installed TES technology uses molten salt as a storage medium, a material that can reach a maximum temperature of 565 ºC. Among the benefits of using this technology are its high technological maturity, high efficiency and relatively high energy density. Its worldwide presence and its technological maturity are owed to its usage in concentrated power plants for electricity production. Yet, in the last years, it has also being adapted to decarbonize the heat consumption in industries.
Issues with molten salt TES
Despite its advantages, molten salt TES have certain drawbacks. Among them is the fact that they solidify at temperatures below 200 ºC requiring constant heating to avoid blockages and maintain operability which complicates system design and operation. Another issue is their aggressive corrosiveness, which increases with temperature. It can degrade metal components such as pipes, heat exchangers, and tanks, necessitating the use of expensive, corrosion-resistant materials, which increases capital and maintenance costs. These issues make molten salts a reliable but complex and costly TES solution and open the door for other technologies to be used instead.
Alternative materials
Considerable research efforts are being invested to drive the circular economy in the field of thermal storage. Construction and demolition waste, ceramics by-product from the treatment of asbestos, or ceramics made of copper slag and red mud are among the considered materials.
Advantages and Limitations of Ceramic Materials
The primary advantage of ceramics for TES lies in their ability to withstand extremely high operating temperatures – often exceeding 1000 °C – without melting, decomposing, or degrading structurally. This makes them ideal for next-generation TES systems designed for use in industrial waste heat recovery, and electrified heat applications. Additionally, ceramics are generally chemically inert, non-flammable, non-toxic, and resistant to corrosion, making them low-risk materials in terms of environmental safety and long-term operation.
Two key thermophysical properties govern their performance as TES media: thermal conductivity and volumetric heat capacity. High thermal conductivity enables faster charging and discharging cycles, improving system responsiveness and efficiency. At the same time, a high volumetric heat capacity allows more energy to be stored per unit volume. The challenge lies in balancing these properties, as many low-cost ceramics (especially recycled types) have low thermal conductivity, which can limit heat transfer and reduce the usable power output of the system.
Ceramics are also brittle by nature, which makes them vulnerable to mechanical stress and thermal shock — especially under fast or cyclical heating conditions. These issues can be addressed through better design of component geometry (e.g., allowing thermal expansion), or by using engineered ceramics and composites.
System Configurations: Packed Bed Thermoclines
Ceramic materials are most commonly used in packed bed TES systems, where the ceramic elements (e.g., bricks, spheres, pellets) are arranged inside an insulated tank. In this configuration, heat transfer fluid (usually air) flows through the voids between the solid elements, exchanging thermal energy with the storage media. This type of system is simple, cost-effective, and mechanically robust.
Figure 2: Thermocline storage tank schematic. Source.
A frequently used approach is the thermocline configuration, where a single tank is charged from one end and discharged from the opposite end, allowing a temperature gradient to form and move through the bed. If more capacity is needed, multiple units are arranged in parallel. This reduces the need for two separate tanks as used in molten salt systems – one for the hot charged salt and one for the cold salt post discharging – and minimizes material requirements and heat losses.
Current Research and Development
Several major European research projects are focused on ceramic-based TES development. These include the FLUWS project, which investigates radial packed bed designs using recycled ceramics or HIFLEX, which explores ceramic storage for renewable combined heat and power plants. Academic institutions such as KTH Royal Institute of Technology in Sweden and CIEMAT in Spain are active in testing new ceramic formulations, thermal cycling behavior, and integration strategies for CSP and industrial heat applications.
These projects often prioritize the use of recycled ceramic materials — including demolition waste and off-spec tiles — to promote a circular economy while reducing costs and environmental impact. Material validation, performance benchmarking, and system-level modeling are common themes across all research activities.
Real-World Implementation: Eco-Tech Ceram and Kraftanlagen
Beyond the lab, several companies have already deployed ceramic-based TES systems commercially. Eco-Tech Ceram, a French company, has developed a containerized storage solution called the Eco-Stock, which uses refractory ceramics to store the heat of the exhaust fumes. This captured energy is then used in other parts of the industrial process. The Eco-Stock is designed for modular deployment, offering up to several MWh of storage in a mobile, insulated unit.
Figure 3: Ecotech Ceram’s system at Tegulys. Source
Another notable example is Kraftanlagen Energies & Services in Germany, which has implemented ceramic TES systems for industrial clients. Their systems use solid bricks or structured ceramic blocks and can be integrated into steam generation systems, heating loops, or combined heat and power plants. They often work with ceramic suppliers to customize materials and geometries based on specific temperature, cycle, and pressure requirements.
Outlook and conclusion
The field of thermal energy storage is dynamic, with new technologies well on their way. Ceramic-based TES systems represent a resilient and increasingly practical solution for high-temperature energy storage, especially when aligned with circular economy principles. As both research and industry continue to validate their performance and durability, ceramics — particularly recycled varieties — are promising a more sustainable future both for our materials and energy usage. With commercial applications already underway and further innovation on the horizon, ceramics are set to play a central role in scaling sustainable, high-efficiency heat storage across industrial and renewable energy sectors.
At FersiSolar we’re ready to help you install the right thermal energy storage at your plant. Contact us, the world cannot wait.